Industrial Camera
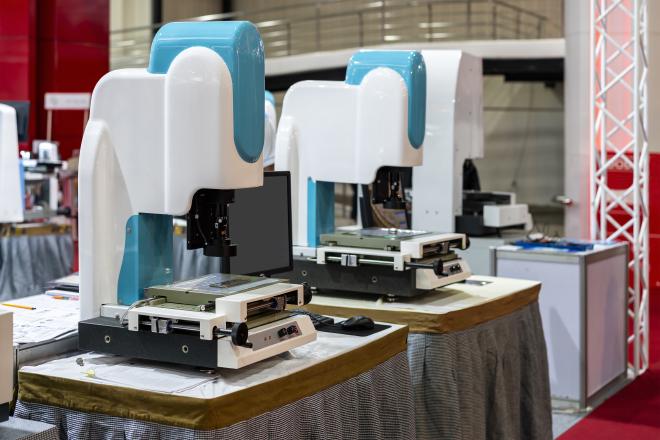
Table of Contents
Industrial Camera for Product Inspection #
Overview #
This project involved designing an industrial camera system for product inspection, utilizing a dual-sensor setup for enhanced optical zoom capabilities. The system was built around a Xilinx FPGA and featured advanced image processing, enabling high-performance frame acquisition and manipulation.
Key Features and Achievements #
- Dual-Sensor Setup: Integrated two identical Sony sensors with different lenses to achieve optical zoom functionality.
- Advanced Image Processing Pipeline:
- Frame acquisition from the Sony sensor.
- Debayering, white balance adjustment, and vignette removal.
- Image zooming and cropping for customized output.
- High-Speed Sensor Interface:
- Operated at the maximum bus speed of the device’s speed grade.
- Implemented dynamic phase alignment (DPA) to ensure reliable communication.
- AXI-Based Architecture:
- Utilized an AXI bus for video data handling, ensuring compatibility and efficient integration of pre-existing Xilinx IPs.
- Memory Management: Processed images were stored in memory for efficient access by a Zynq processor.
- High-Speed Transmission: Images were further processed on Zynq and transmitted over Ethernet for real-time analysis.
Technical Details #
- Hardware: Xilinx FPGA, Sony sensors, Zynq processing unit.
- Development:
- Designed and implemented the FPGA architecture in VHDL.
- Verified using SystemVerilog testbenches.
- Integrated pre-existing Xilinx IP cores into the design.
- Technologies Used:
- Xilinx Vivado for synthesis and implementation.
- Verilog/SystemVerilog for verification.
- AXI bus for internal video data routing.
- Image Pipeline: Acquired and corrected images stored in memory before being accessed by Zynq for further processing.
Challenges and Solutions #
- High-Speed Communication: Overcame bus speed limitations by implementing dynamic phase alignment (DPA) to maintain reliable sensor communication at maximum speed.
- AXI Integration: Successfully adapted the design to incorporate pre-existing Xilinx IP cores, leveraging the AXI protocol for efficient video data handling.
- Synchronization: Managed synchronization between two sensors for seamless optical zoom integration.
- Processing Efficiency: Optimized FPGA resources to handle the entire image processing pipeline without bottlenecks.
Outcome #
The camera system delivered exceptional performance in industrial product inspection, leveraging dual-sensor optical zoom and real-time Ethernet transmission. Its robust image processing pipeline, AXI-based architecture, and high-speed communication met demanding industrial requirements.